Cantier Systems
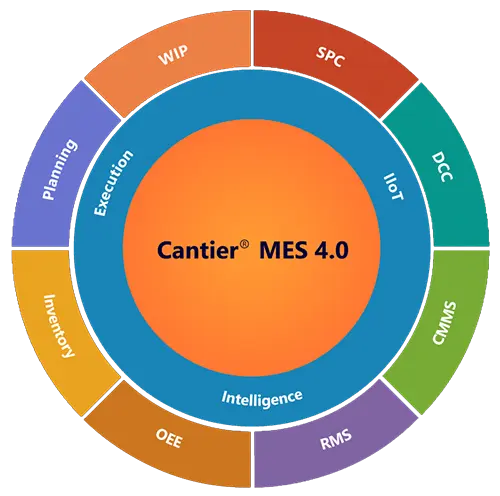
Experience Industry Specific,
Modular And Configurable Mes 4.0
Solutions That Achieve Rapid Roi.
Our solutions have shown significant improvements
in manufacturing Shop-floor Traceability, Visibility,
Quality, and Overall Equipment Effectiveness (OEE)
leading to Real-time flow of accurate information
towards Data-driven decisions.
Cantier Manufacturing Intelligence built with
Machine learning predicts equipment downtime,
parts failure, and potential quality issues, unlocking
the contextual data from the shop floor equipment
and devices to deliver significant business value to
our customers.
MES 4.0 Modules
- Integration with RFID, QR Codes & Barcodes
- Supports Production Kitting, Material Returns & Inventory Adjustments
- Provides item tracking by lot number, serial number and expiration date
- Locations can represent warehouses, areas, bins, trucks, etc.
- Shop calendar for work days and holidays
- Automatic work order/job order generation directly from the production scheduling
- Finite Scheduling
- Backward scheduling from the required dates of the customer
- PO generation from net demand relative to reorder levels
- Traceability & Genealogy
- Track any product past or present
- Real-time Visibility
- Product Costing
- Paperless Transactions
- Improved Cycle time & Reduced Manufacturing Cost
- SMART Production
- Data Collection, Extraction & Export
- All Standard Variable Control Charts (i.e.: Xbar R, XbarS, etc.)
- Monitor key independent and dependent variables from the process
- SPC automatically calculates control chart limits
- Automatic Equipment shutdown for Out of Control Situations.
- Eliminates the need for paper routing.
- Cycle time & labor productivity improvement in critical business processes.
- Can be used as a tool to measure approvers’ speed of execution.
- Drives compliance to ISO, QS, and regulatory, legal and other standards.
- Improved Traceability.
- Breakdown, Scheduled and Predictive Maintenance.
- Tracks machine or tool conversions and set ups
- Analysis to identify maintenance & technician’s training issues
- Predictive Maintenance avoids the Machine breakdowns
- Reduce dependency on Reactive Maintenance
- Predict Machine Breakdowns
- Real-time Dashboards with Drill-down details of Equipment OEE
- Productivity Improvement with Real-time data
- Minimize breakdowns and Reduce repair Cost
- Increase Competitiveness & ROI
- Track, monitor and validate the recipes realtime
- Reduce operator errors
- Reduce Quality issue
- Lot traceability using QR Code or RFID associated with corresponding Recipe ID
WIP-Track and Trace
Cantier WIP Traceability enables the
manufacturer to track material in the
production floor and keep record of the parts
source, material certificate, number, batch
number, date of manufacturing, inspection
date, and etc. This lineage facilitates quick
recall of the identified defects and prevent
further damages or failures.
Benefits
- Traceability & Genealogy
- Real-time Visibility
- Product Costing
- Paperless Transactions
- Reduced Cycle time & Manufacturing Cost
- Merges multiple lots of the same product in the same operation step
- Reworks defective units including the replacing of defective parts
- Generates online history of lots processed
- Transfer to FG to close lot in WIP
Cantier WIP Traceability captures the relevant data as part of the lot history including:
- Batches/serial ID of material components used and replaced
- Operator who worked on the lot
- Machine/Tool ID used in the process
- Defect/Rework breakdown
- Adequate data to correlate product quality with process parameters that drive continuous process improvement
Smart Quality Management with SPC
SPC monitors the performance of a process and, using statistics, helps identify trends and variation to
prevent the process from going out of control.
Cantier SPC with the intelligence capability to collect and analyze real-time data, based on user defined tests, helps draw smart conclusions. Hence manufacturers can make data-driven decisions to improve product quality, reduce risk, and to meet compliance requirements. With the machine learning features, Cantier SPC provides Predictive Quality based on the historical data.
Cantier SPC with the intelligence capability to collect and analyze real-time data, based on user defined tests, helps draw smart conclusions. Hence manufacturers can make data-driven decisions to improve product quality, reduce risk, and to meet compliance requirements. With the machine learning features, Cantier SPC provides Predictive Quality based on the historical data.
Automated And Synchronized SPC With MES & IoT
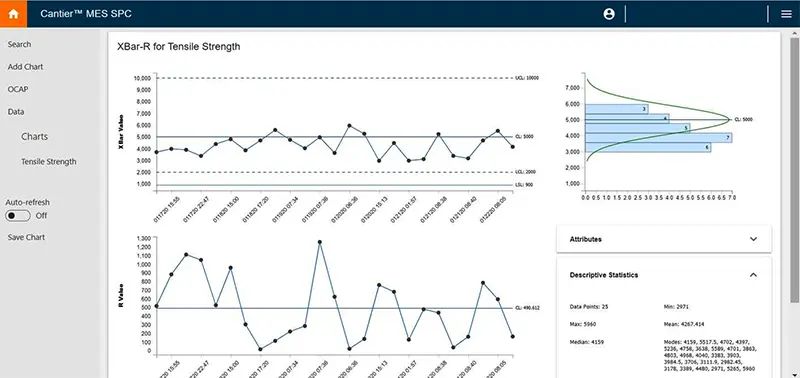
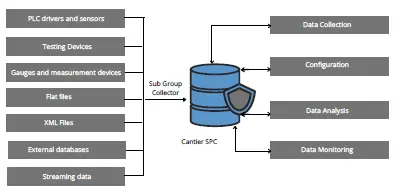
Key Features
- All standard variable control charts (i.e. Vbar R, XbarS, etc)
- Descriptive statistics (i.e. Xbar R, S, Cp, Cpk, Skewness, Kurtosis, etc.)
- Graphical representation (i.e. Frequency Distribution, Pareto, etc.)
- Independent and dependent process variable monitoring
- Quality history for root cause analysis
- Continuous data acquisition from multiple production and Inspection work centers
- Automatic control chart limits calculation.
- Analysis for out of control and automatic equipment stoppage
- Auto notification via screen, email, or SMS for out of control condition.
Document Control Center (DCC)
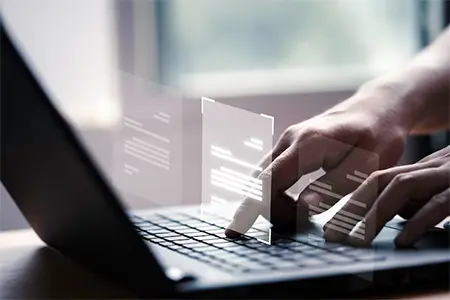
Cantier Document Control Center (DCC) solves manufacturing document management problems. DCC
centralizes all documents and ensures the availability latest revision of document to all the modules of
Cantier solution. DCC can accept multiple document formats such as, CAD/CAM Files, MS Word, MS Excel,
PDF, as well as photo formats, video formats and others.
Document Types Handled:
- Raw material and manufacturing specifications
- Customer and internal control plans
- Engineering drawings.
- Standard operating procedures
- Setup checklists
- Equipment maintenance procedures and checklists
- Packaging and labeling instructions etc.
Key Benefits
- Eliminates the need for paper routing.
- Cycle time & labor productivity improvement in critical business processes.
- Can be used as a tool to measure approver’s speed of execution.
- Drives compliance to ISO, QS, and regulatory, legal and other standards.
- Improved Traceability.
- Drives document standardization across the factory.
- Helps position the factory to be Audit Ready at all times.
Maintenance Management
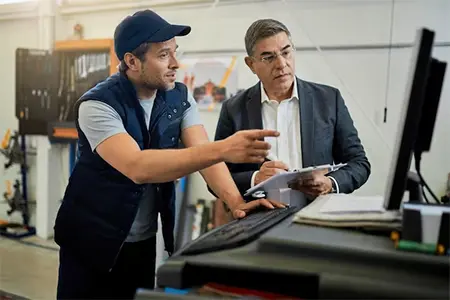
Cantier CMMS helps to track, predict and improve equipment performance in the factory.
Apart from Corrective and Preventive maintenance Cantier solution includes Predictive capability which
can be Usage based or Condition based activities using the real-time IIOT data. Machine Learning models
based on the historical data predicts equipment failures and proactive maintenance incidents.
Features
- Work Order Management
- Equipment Logs
- Equipment Problem
- Knowledgebase
- Spares Requirement Planning
- Maintenance KPIs
- OEE
Key Benefits
- Provides tools to track, predict and improve equipment performance
- Manages scheduled, unscheduled equipment maintenance and predictive maintenance
- Predictive maintenance includes Usage and Condition based maintenance with real-time
- IIOT data from OT devices
- ML models predict equipment failures and maintenance incidents.
- Helps to monitor KPIs such as MTBA, MTBF, MTTR, OEE
Recipe Management System (RMS)
Automatically selects the right recipe for a particular Lot or Batch
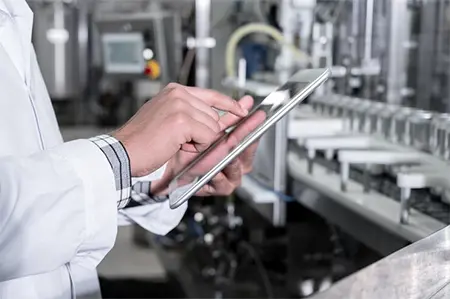
Recipe Management System (RMS) plays a vital role in SMART Manufacturing when it is completely
automated with two way communication between Equipment and MES. RMS is tightly integrated with
the Product Configuration and it allows to identify the right recipe automatically when the lot or Batch
move to a station or equipment. It provides alert or even stop the machine when there is wrong recipe
selected by an operator.
RMS validates the recipe data against Lot or Product or equipment quickly and download or upload
recipe files to SEC/GEM supported machines. Also, it allows to download or upload recipe parameters to
PLCs. This validation and real-time upload and download features prevent faults, increase throughput
and yield. It helps to compare parameter values between different versions of recipes in real time and
historical values as well. Reports available to compare the performance KPIs against different versions of
recipes.
RMS maintains a centralized Recipe Library across the factory to store and transact the recipes securely.
With the help of Cantier SPC, Recipe parameters vs Output parameters is monitored real-time and
provide the trend report. When there is a downward trend, RMS alerts the users to look at the recipe
values for adjustments.
Overall Equipment Effectiveness (OEE)
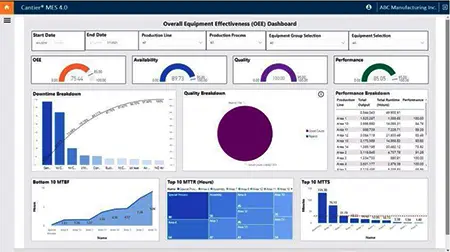
By accurately measuring OEE with Real-time data, companies can quickly see how effectively a
manufacturing operation is utilized and thereby establishing continuous improvements in the factory by
eliminating wastes. The three components of OEE are Availability, Performance and Quality.
Availability
It represents the percentage of planned time that the operation is available to operate. Availability accounts for all the losses that happened during the planned production time such as equipment failures, material shortage, setup time, etc. Cantier OEE measures availability information from CMMS module and real-time communication with the Equipment through OPC, OPCUA, SECS/GEM communication protocols. Cantier IIoT gateway securely manages all these communication and data collection. Downtime logs are captured and alert the operators as it happens.
It represents the percentage of planned time that the operation is available to operate. Availability accounts for all the losses that happened during the planned production time such as equipment failures, material shortage, setup time, etc. Cantier OEE measures availability information from CMMS module and real-time communication with the Equipment through OPC, OPCUA, SECS/GEM communication protocols. Cantier IIoT gateway securely manages all these communication and data collection. Downtime logs are captured and alert the operators as it happens.
Performance
The actual cycle time vs Ideal Cycle time data is analyzed. Performance is calculated from how much waste is created when running at less-than-optimal speed.
Cantier OEE measures the performance by collecting the actual cycle time directly from the machines and compares it with the ideal cycle time defined in the Product configuration and Equipment set up. Real-time communication with the equipment provides accurate performance real-time.
The actual cycle time vs Ideal Cycle time data is analyzed. Performance is calculated from how much waste is created when running at less-than-optimal speed.
Cantier OEE measures the performance by collecting the actual cycle time directly from the machines and compares it with the ideal cycle time defined in the Product configuration and Equipment set up. Real-time communication with the equipment provides accurate performance real-time.
Quality
Measure of the Good Units produced as a percentage of the Total Units Started. Quality loss include scrap or defect and units that need rework.
Cantier OEE measures Quality by collecting the data from the WIP module and directly communicating with Metrology equipment through IIoT Gateway.
Measure of the Good Units produced as a percentage of the Total Units Started. Quality loss include scrap or defect and units that need rework.
Cantier OEE measures Quality by collecting the data from the WIP module and directly communicating with Metrology equipment through IIoT Gateway.
Cantier IIoT
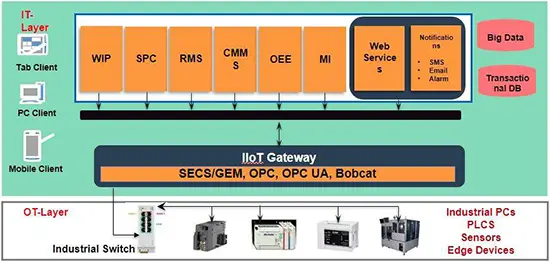
Cantier IIoT establishes the communication among systems and devices using specific OPC, UPC UA,
SECS/GEM and Bobcat Drivers. Through this communication, MES Application modules and Equipment
controllers or Equipment PCs can exchange data for real-time controls and provides alerts when there
are out of control situvations such Equipment Breakdown, Recipe and quality parameters. Cantier IIoT
helps to collect the data from various type of devices across factories to store large volume of data over
network or cloud repositories to enable predictive and big data analysis.
KEY FEATURES
- Ability to connect and collect data from Industrial PCs, PLCs, Sensors, Edge Devices and others
- OPC UA, MQTT, SECS/GEM Protocols for communication as Industry 4.0 standard
- Core and Edge Architecture for handling large volume of data traffic and provide Edge Analytics
Manufacturing Intelligence (MI)
Cantier Manufacturing Intelligence (MI) analyzes the data with manufacturing context and enables to
take data driven decisions at the shop floor with KPI-based dashboards and reports. It communicates
across systems and performs autonomous actions. Cantier MI also predicts potential issues by applying
artificial intelligence and machine learning technology.
KEY FEATURES
KEY FEATURES
- Alerts and Notifications
- Proactive Decision Making
- Make timely decisions with KPI based dashboards.
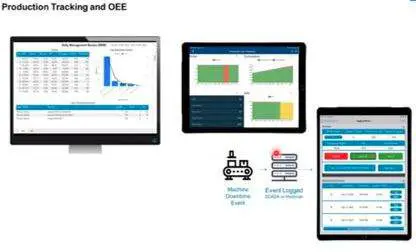
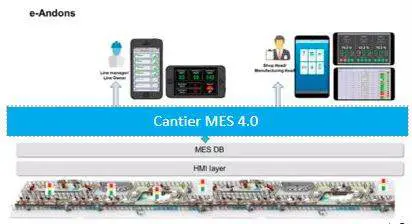
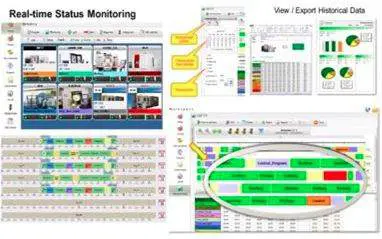
Advanced Planning and Scheduling
Cantier provides Advanced planning and scheduling with integrations to ERP solutions .
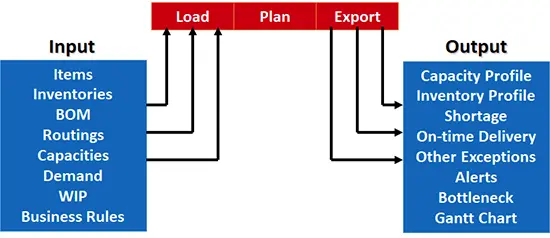
Capacity Constraints Handled
- Throughput, Setup, Wait and Queue Time
- Working Shift, Non-Working Shift & Over Time
- Planned and Unplanned Machine Down Time
- Alternate Resource
- Alternate Routing
- Batch, Subcontract, Pooled and Additional Resource
- Sequence Dependent Setup Time
- Yield
- Campaign
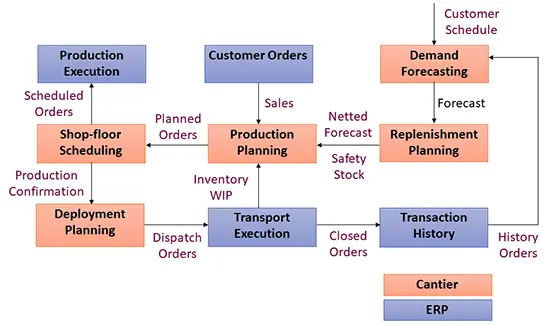
Material Constraints Handled
- Lot Size
- Material Availability
- Transfer Batch Quantity
- Alternate Item
- Material Reservation
- Customer Due Date
- Consolidation
- By Products
- Operation Level Consumption
- Supplier Fair Share
- Solvent Recovery
- Routing Based Consumption